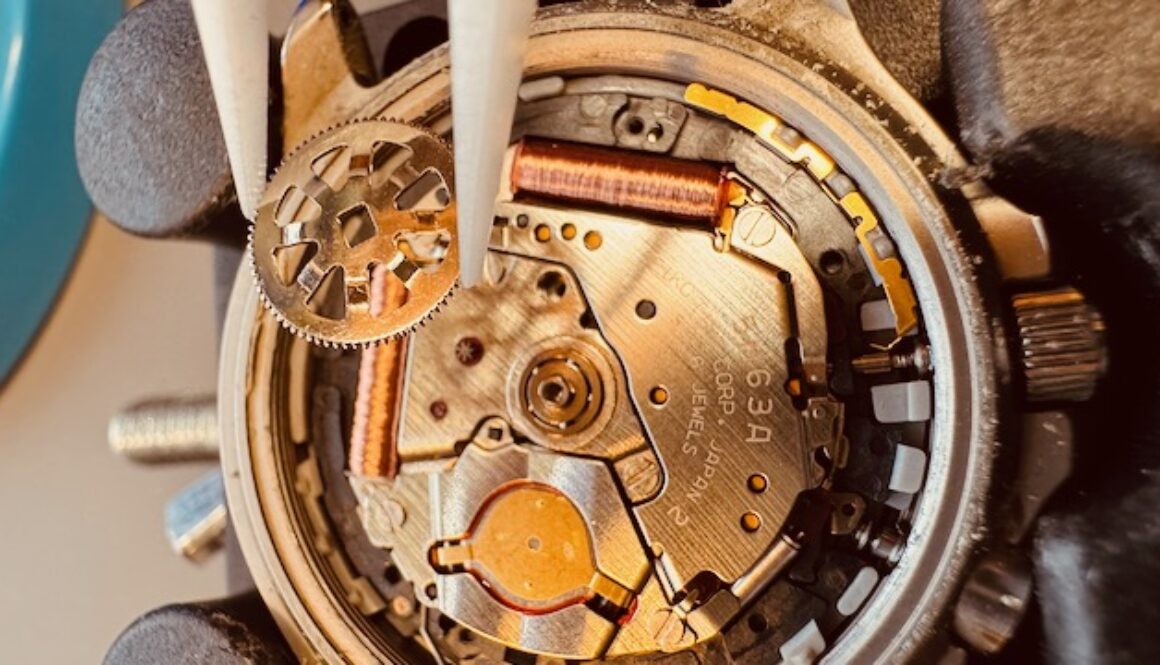
Electronics
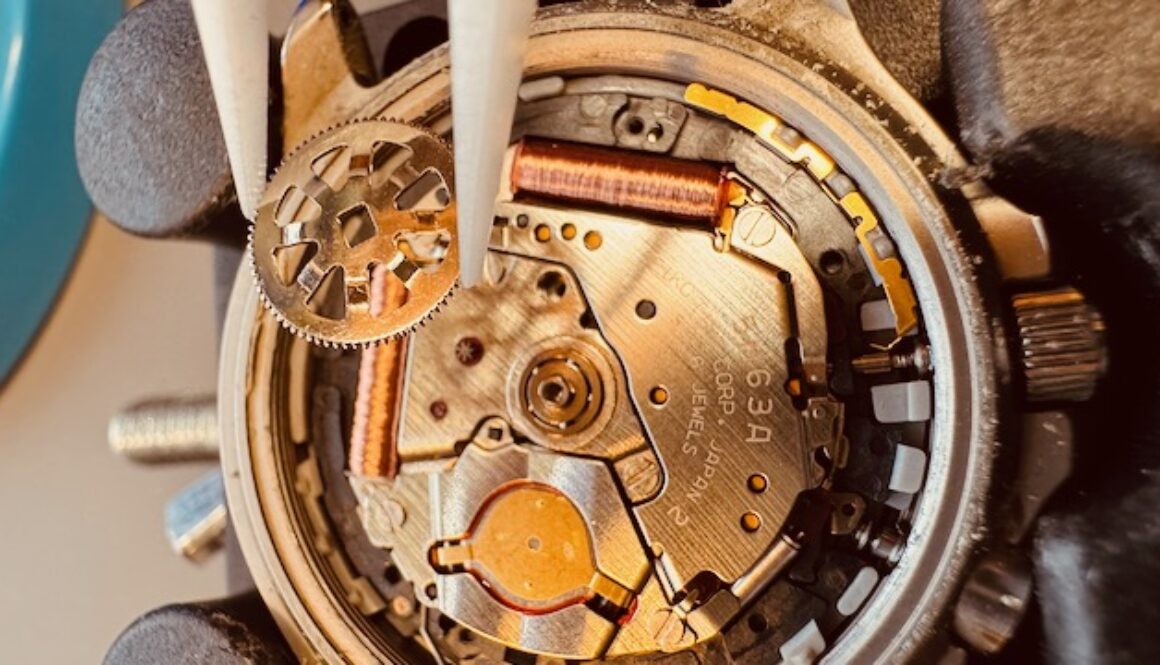
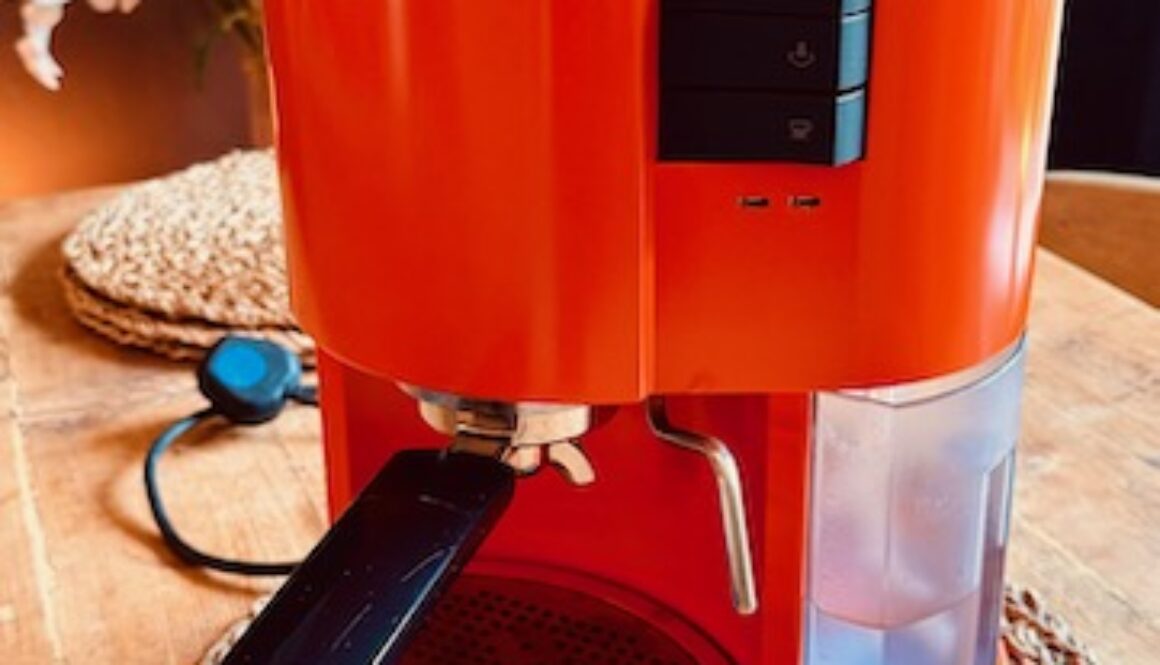
Gaggia Carezza Silver 2002
Below are the refurbishment photographs of a 2002 Gaggia Carezza Silver. This is the early model of the cheaper nastier Carezza which came later. This early model was more akin to the Gaggia Classic, with an almost identical boiler and purely mechanical internals. It did not however have a three way valve solenoid, instead using an overpressure valve built into the boiler head itself.
This was purchased to be a refurb project and side machine to have a retro 60’s look. In the end however after it saw little use I decided to sell it and it has now gone on to a new coffee enthusiast home.
The machine was stripped, cleaned, descaled and rebuilt following a sand down and respray. The design of the water tank made keeping the paintwork of the machine difficult as it tends to be such a tight fit. We also discovered a nut that forms part of the overpressure valve is missing. The machine does however still make excellent espresso and hopefully has a new lease of life.
As purchased. Initial descale in progress.
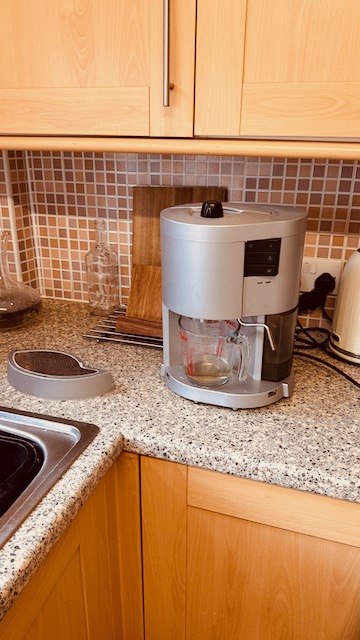
Click on image to enlarge.
Above shows the boiler during its clean. In really good condition and no corrosion at all on the shower screen.
Cleaning up the insides
The above gallery shows the plastics prior to cleaning and repainting. This is the larger 1425w boiler.
Setting the pump pressure
Pump pressure setting is a little more primitive on these machines and involves adjusting a small screw. This easily corrodes and I was lucky to be able to move this one to set it to 9 bar for best extraction.
Finished machine
Finished machine painted in RAL2004 orange.
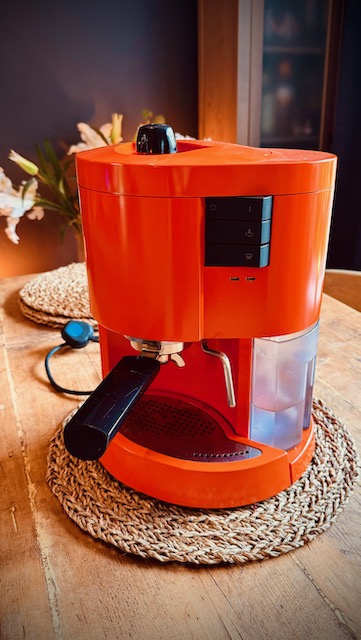
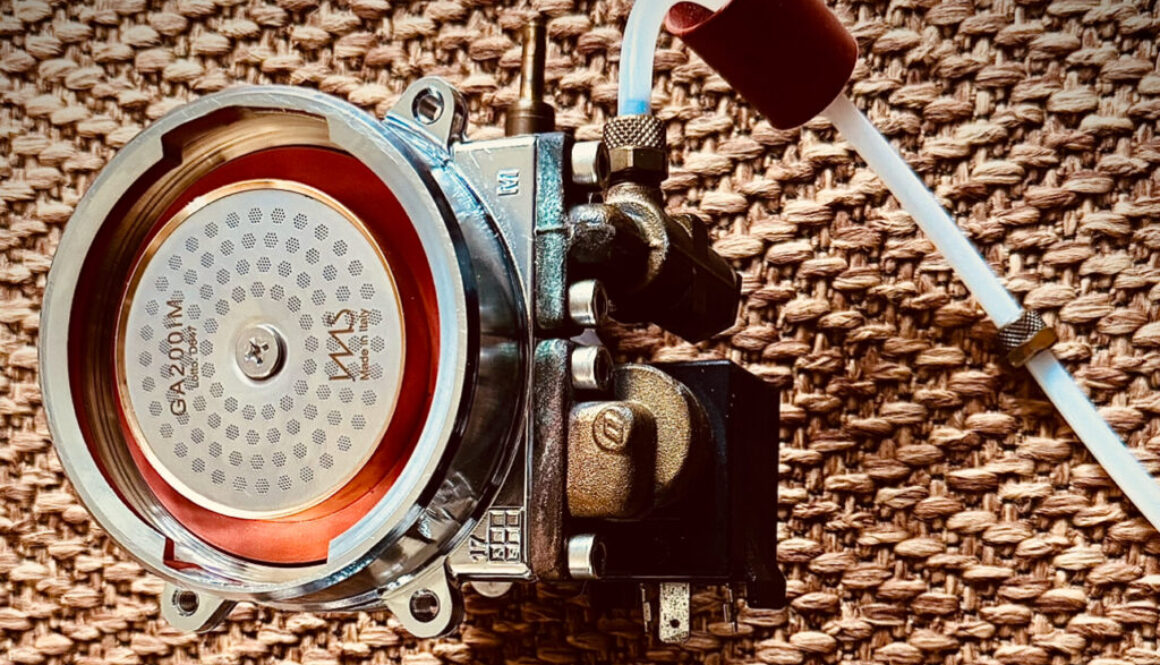
Gaggia Classic Boiler Replacement
This article documents the replacement of a boiler from a Gaggia Classic. It is a 2005 model, and whilst it has generally been serviced well over the years, the boiler has, over the past year become unserviceable. This is mostly in part due to corrosion from the aluminium dispersion plate that has become welded to the group head, and despite removing the boiler entirely and using some fairly industrious methods to separate the two, the results have merely been to damage the dispersion plate further.
I had therefore made the decision to replace the entire boiler; which was also in a fairly bad way, and also the group head, dispersion plate and all the associated seals. The following shows images of the work necessary and the improved performance.
Taking the lid off there is plenty evident corrosion around the 3 way valve and the case.
All the wires were labelled ready for the loom to be removed. It’s easy to muddle up cables, so to save confusion later, it’s worth labelling each cable if the loom is to be removed entirely.
Below shows the condition of boiler on removal
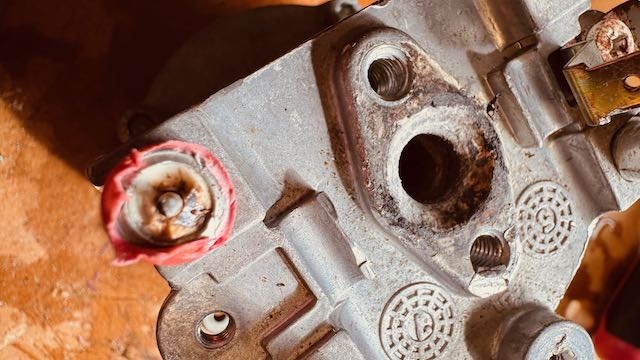
Previous damage to the boiler had resulted in an element pin being broken off. This was patched by soldering directly to the element.
Once all the components have been removed the case could be cleaned up and a new plug crimped onto the loom for the broken pin.
Above shows the condition of the vibratory pump bush that prevents too much noise and case vibration. This was replaced with new, and the pipes removed and soaked in Cafiza to remove the stains and residue. The pump and rubber bush is held on to a metal plate via a clip that is then screwed to the case.
Opening the old boiler was necessary to remove the 48mm copper boiler pipe inside. It was also interesting to see what condition the internals were left in after a period of neglect. The boiler was opened with an angle grinder cutting through the bolts as these were firmly seized.
Assembling the new boiler.
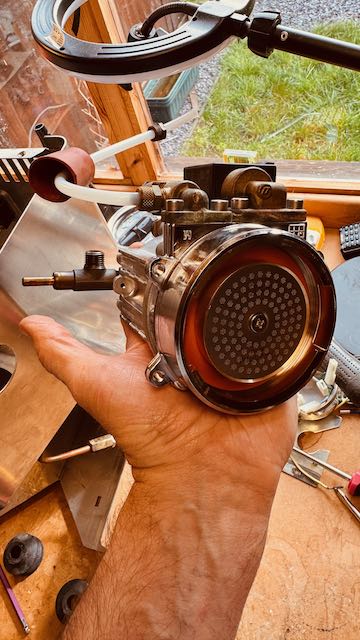
Assembled Boiler using the Italian made IMS 55mm GA200IM Competition Shower Screen and Silicon Gasket
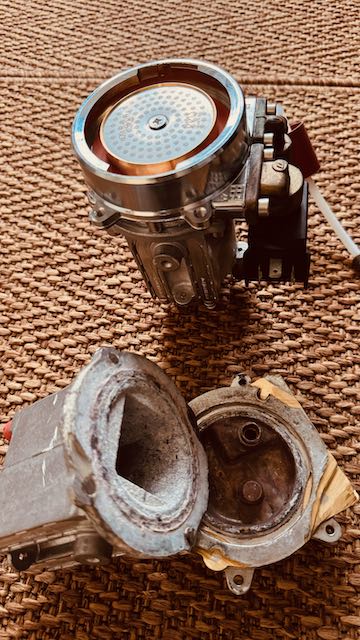
Ready to be rebuilt.
Cleaned and reassembled ready for the dreaded leak test !
Up and Running !
Steam Power
Mazzer Super Jolly Refurb
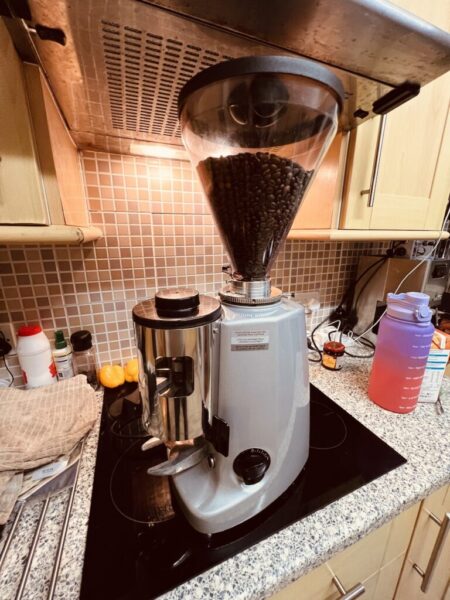
Following 7 years of using a Carimali G1 grinder I bought two Mazzer Super Jolly grinders to refurb and modify to doseless versions. One SJ came from a Café in Corby that had upgraded to digital dosed grinders, whilst the other one was from a home user on Facebook Marketplace.
Both Grinders had a few issues and had needed a bit of TLC.
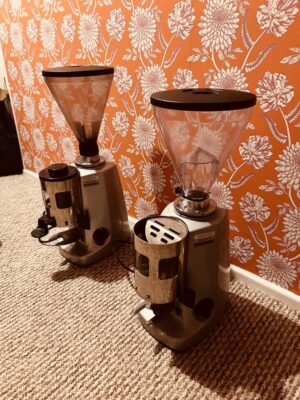
One is considerably newer than the other with slightly different design. The lids have different designs, but most notably is the switch which comes in either a push to start version, or a timer version. These two machines had different switches. The intention is to put one of these grinders on a separate grind timer device, so using the one with a timer switch made more sense as this can be easily adjusted to stay ‘on’ permanently’ without modding or cutting the case of a new switch.
The doser has a slightly different appearance in the shield above the grinds chute. Other than that the machines are almost identical.
Starting the Strip Down
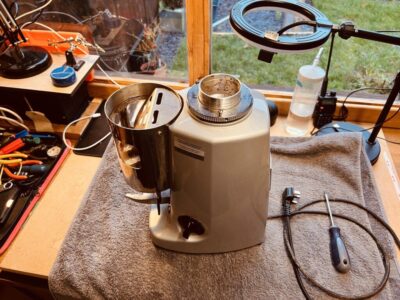
64mm Mazzer Burrs
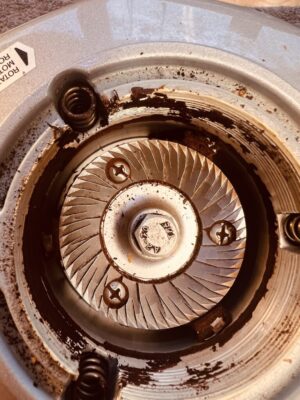
- 350w Motor
- Inside Motor can be Disconnected
- Similar wiring to the Gaggia Classic
Wiring colours inside are similar to the Gaggia Classic with pale pastel colours. The motor can be disconnected with a plug and the only other connections are a neon lamp and a timer switch which has a couple pole switch that breaks both the neutral and live.
- Cable Replacement
- Old Cable
The original cable had had its day. The outer insulation was brittle and ready to crack. The plug top had the wrong fuse and a missing fuse cover. The entire cable was removed and replaced with a new one.
- Burrs
- Dirty Burrs
- Dirty Burrs
- Cleaning Time
- Doser
- Doser Cannister
Anything that could be soaked in Cafiza at this point was soaked and refreshed to its original sparkly appearance!
Sparkly Parts!
- Sparkly Parts!
The doser spring had snapped after years of use. These are easily replaced but can easily be temporarily repaired by bending the far element of the spring back round the spring holder.
Once everything was cleaned and the machine blown out with an air compressor it was time to start putting everything back together again.
The lower burr carrier is the only tricky part. This slides on to the hub of the motor spindle. However it MUST line up with the notches at the base of the carrier, else it will not go all the way to the bottom and you will have to work at getting it off again which is not easy without a puller.
The above images show how close the burr teeth get to each other without touching.
The timer switch and surrounding decor was screwed back on. The screws go directly into the timer switch. The timer was locked off inside so that it does not count down and remains in the ON position ready for the external timer.
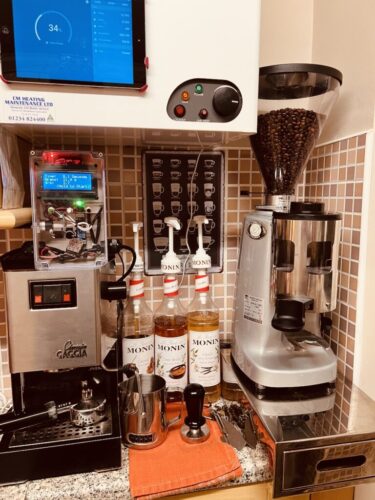
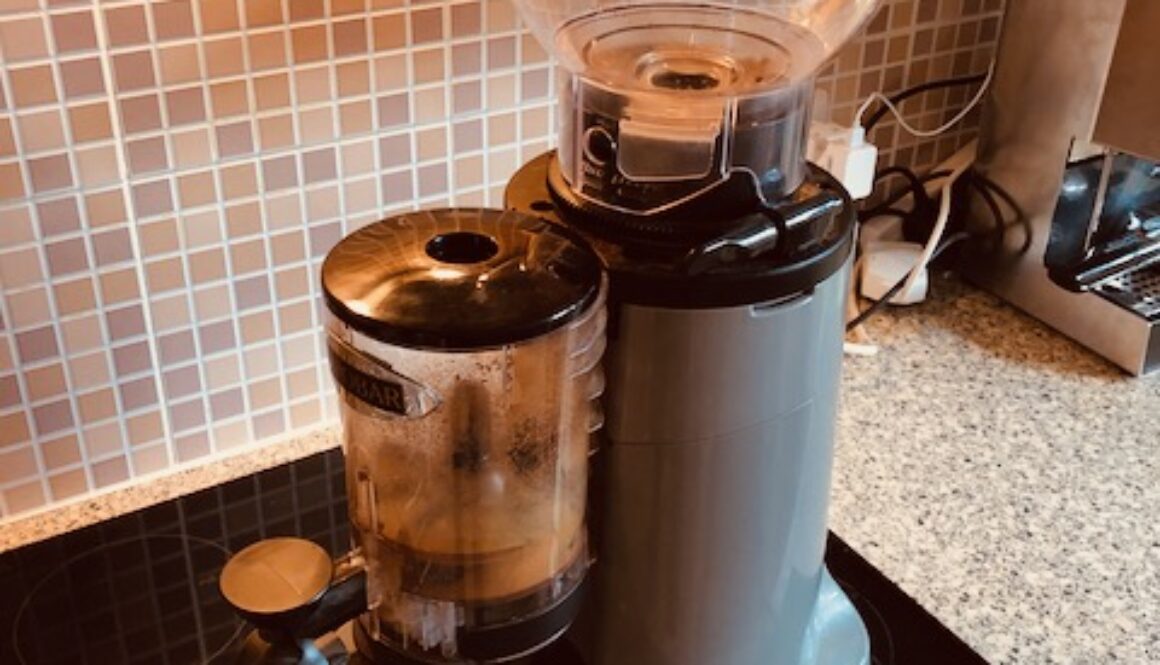
The Great Expobar Grinder Refurb
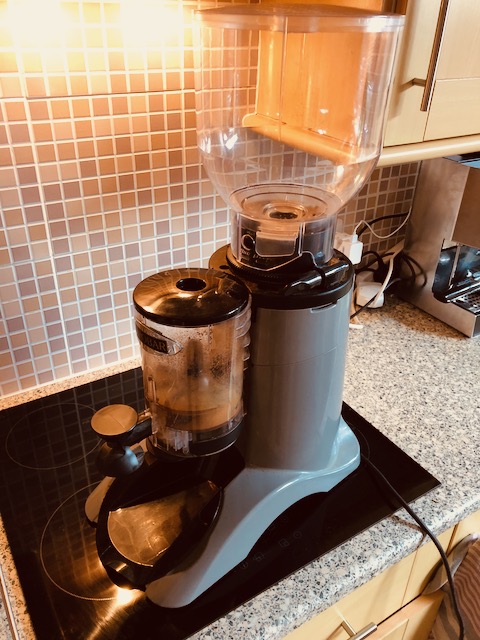
This page documents the complete refurbishment of a Cunill (Expobar) commercial coffee bean grinder. Purchased from Facebook Marketplace for £80 the machine is in reasonable condition and appears to be working. I don’t believe it has seen much maintenance through its life, and there is evidence of enormous build up of coffee oils and grinds throughout the internals of the machine.
The Expobar Grinder is manufactured in Spain by Cunill and generally considered a very high quality well build machine capable of heavy use. The 60mm burrs effortlessly grind coffee to an extremely fine grind, containing a large 275w AC motor.
The aim of this refurbishment is to entirely strip the machine, clean, replace consumable parts/burrs and rebuild, with a newly painted white body.
Below are a series of photographs and captions of progress so far.
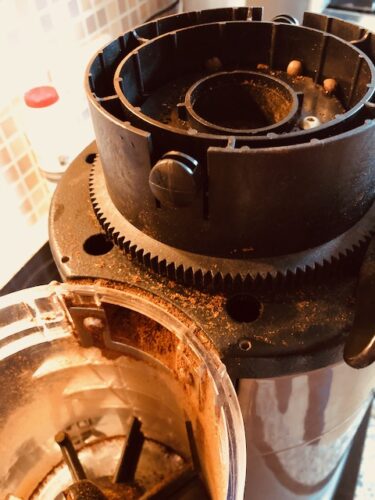
The Hopper Mount / Adjuster. This grinder features a fine tuning thumb screw for unlimited grind settings. Other similar grinders are often 'stepped' making finding the exact grind difficult.
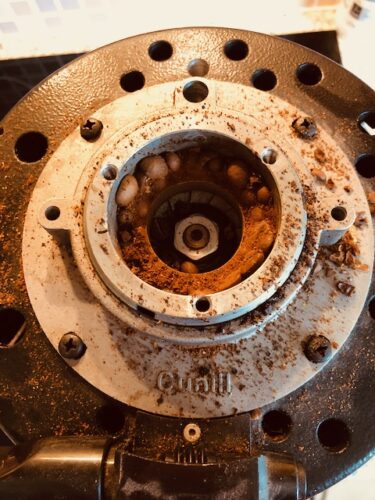
The top Burr is screwed directly to the cap of the grinder. See below for underside view.
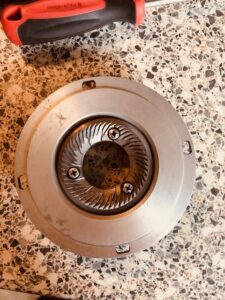
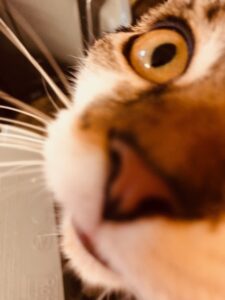
The bottom view of the top burr. Elvis the Kitten getting involved in all new projects.
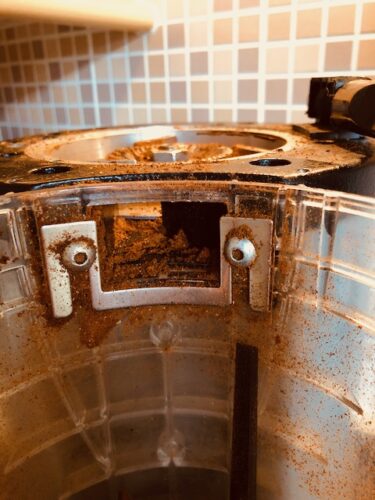
The next difficulty was removing the grinds bin/dispenser. The mechanism is secured by three screws. The top two screwed were seized in and attempting to remove these Allen key bolts risked rounding off the heads. Rotating them half a turn allowed a pair of pliers to do the rest of the job. These will be replaced on reassembly.
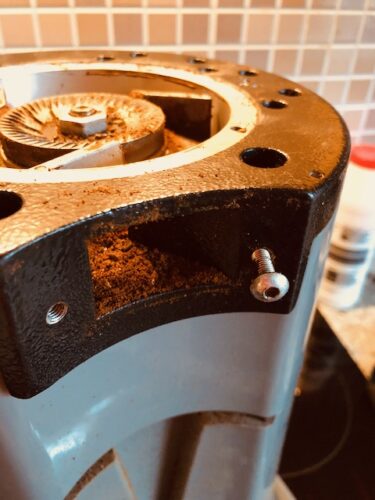
The grind dispenser on this machine is short leading to less wasted grinds between grind and grind collector. This prevents stale beans being collected, or the need for excessive 'purging' of beans before dispensing. This protruding bolt was seized in and removed with pliers.
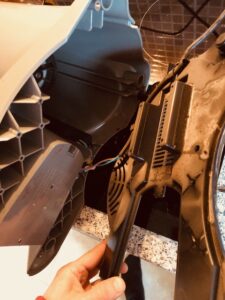
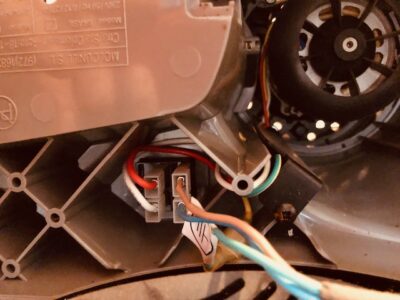
Removing the base of the machine reveals the electrics. This is a simple set up with direct connections through a double pole switch direct to the motor. Earthing connects to the body of the machine.
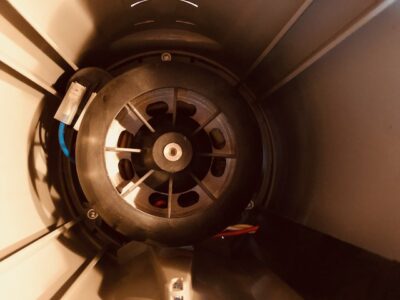
Looking down in to the body of the machine from below reveals the motor and head bolts which are around 4 inches long. These clamp the head of the machine to the base and are difficult to remove. Using a long Allen key and extension bar removing these is a slow laborious task.

The motor finally removed with the bottom burr still attached by a 17mm bolt. Locking the motor allows easily removal of the burr. The motor is generally well sealed from stray grinds, but is blown out with high compressed air.
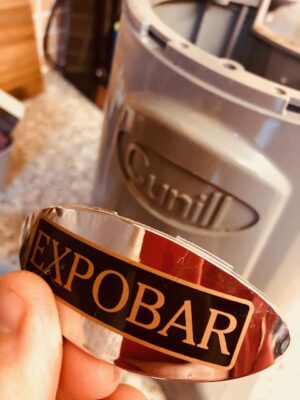
Removing the front badge reveals the true manufacture below. A literal rebrand!
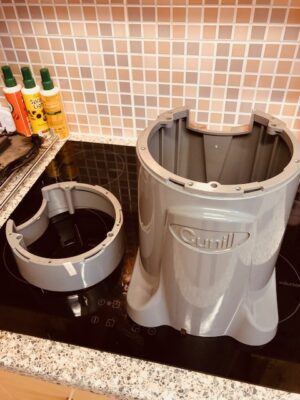
The body of the machine fully removed ready to be prepared for painting.
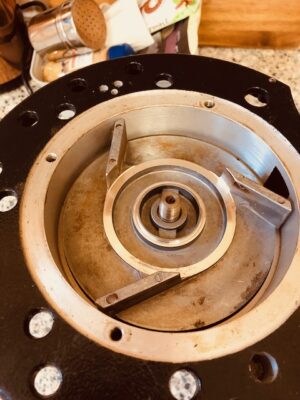
The bottom burr removed.
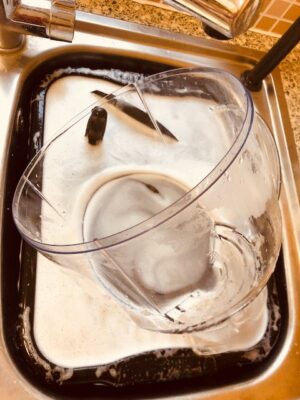
All of the components exposed to coffee are soaked in Cafiza 2. This product effectively strips away all coffee oils and stains and brings the surfaces up spotlessly clean.
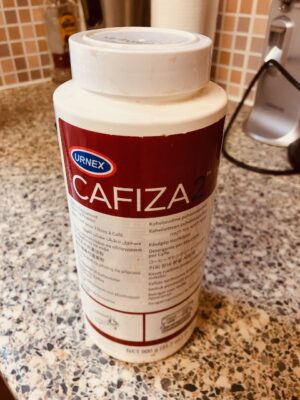
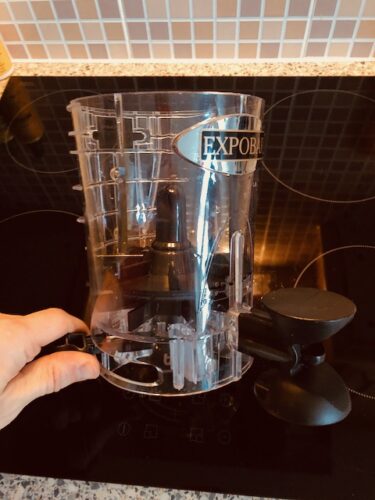
The magic of Cafiza 2. Appears brand new
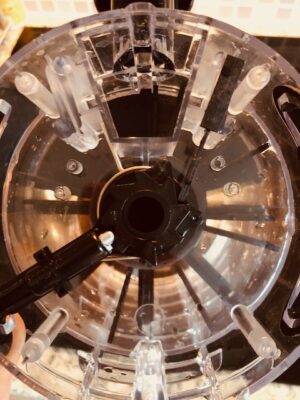
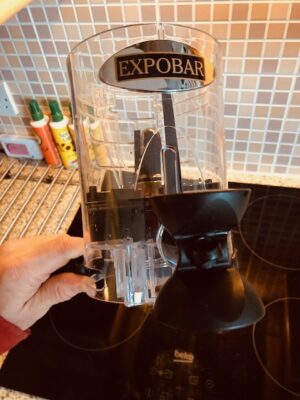
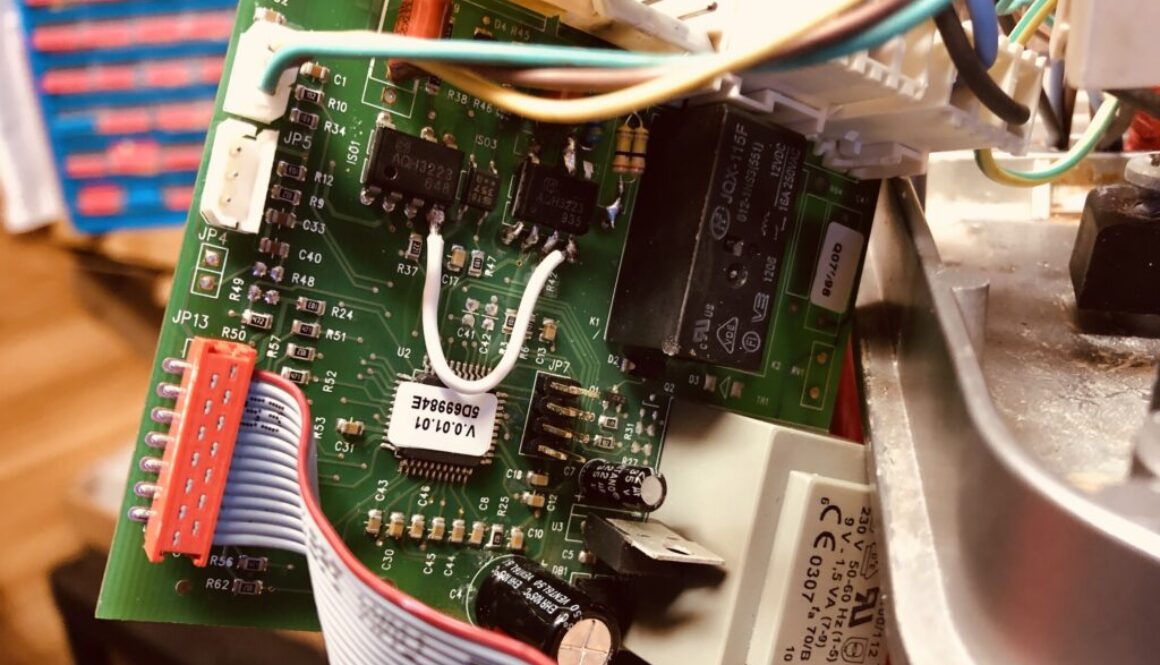
Brought back from the Dead! The Gaggia Baby Dose MAJOR repair
A friend recently bought a ‘new’ coffee machine from eBay for 35 pound. This was a Gaggia Baby Dose which typically, when working sell for between 120-250 pound. When purchased, the seller advertised it as ‘tripping the electrics’ when switched on. This is often caused by a water leak sending current away; so he took a gamble and decided to purchase it with the intent of it being a quick repair.
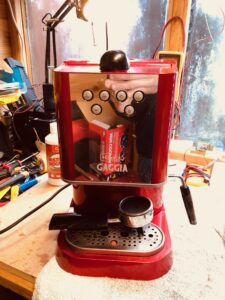
When it arrived he swiftly dismantled it and indeed found evidence of water leakage, but more worryingly there was evidence of burnt out components on the control board. I am not a fan of coffee machines with control boards. Manual switches controlling individual parts of the machine are far more reliable. Steam and high pressure water, a centimetre or two from mains voltage rarely ends well if there are even the slightest of fault conditions. He brought the machine over to the workshop and we started work on a repair.
The aim of this repair was not to end up spending as much as a working machine. So many of these repairs may beckon the question, ‘why not just buy a new component’, but this defeated the purpose of the project, which was to fix the machine at little to no cost. In fact in total the repair bill totalled parts at less than 15 UK pounds.
Control Board
Initially we labelled and dismantled all components to examine their condition. The control board was made up of a low voltage / high voltage separated control board with solid state relays between the two. One controlled the pump/solenoid, and the other controlled the heating element. It was obvious one solid state relay had completely burnt out taking with it the capacitor/resistor network nearby. Several components were either missing or crumbling in smokey remains. By examining a photograph of a replacement board found online we were able to establish the values of the components and order replacements cheaply from eBay.
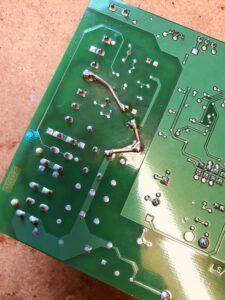
Several components including the Solid State Relay IC and the supporting resistors were changed for 1/4 watt through-hole versions.
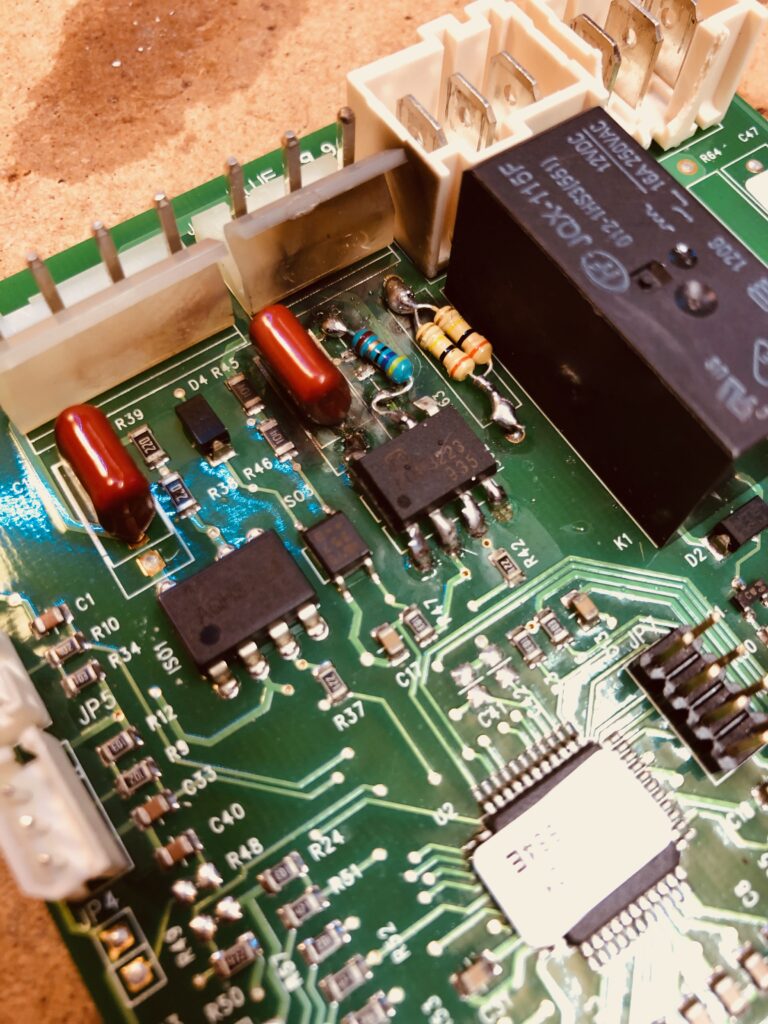
The components were replaced, and the machine fired up. Nothing. Dead as a dodo. Starting systematically with a multimeter, I checked the voltage at the switch which showed voltage at the terminals but one side of the DP switch was not connecting. Removing the switch showed a previous attempt at a repair. A blob of solder had been crudely applied to one side of the connector to try and establish at better connection.
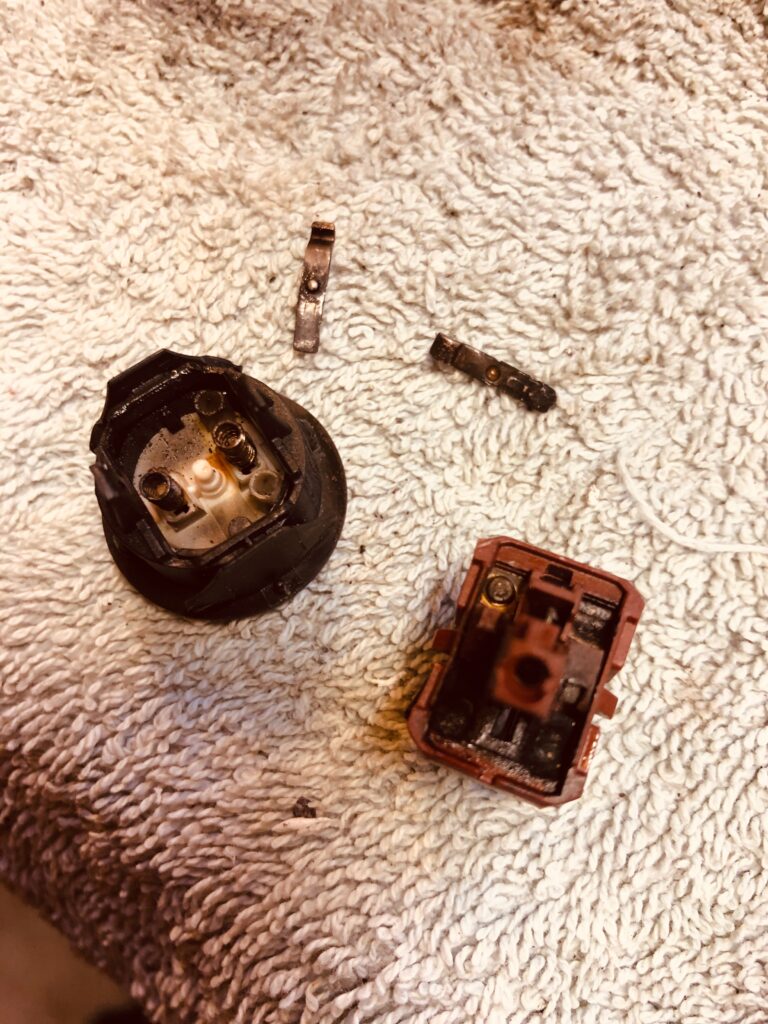
It was clear this switch had called it a day. Fitting a new switch was a little tricky. Replacing the switch with an original part would have been at significant cost, so it was time for some case modifications to install a standard robust DP square switch in a round hole. A bit of gentle work with a hacksaw saw the switch fit in nicely. Sadly the spade connectors did not fit, so off they came and new ones crimped on. We had power to the board! (And a nice light up switch as a bonus!)
Hm, a problem astronauts have had in the past. Hot melt glue to secure the switch Replaced spade connectors Not perfect, but a working switch for £4!
Power up! We have flashing lights on the front panel. The ‘heating’ lamp was flashing. (More on this later), and the heating elements are heating. Good news so far.
So we filled the tank with water and dare to hit the pump button.
There was noise. Lots of it. And heat! Good signs for coffee, but alas no water fell from the group head. Water did spray all over the inside of the machine however. The steam wand was also functioning okay. So why no water from the grouphead?
First thing to do was strip the boiler apart and see if we have a clear path for the water to run. The boiler was not in good condition, and nor were the rubber seals:
Inside the boiler chamber So much corrosion, getting this cleaned up would be difficult The grouphead before cleaning. The shower plate corrosion The thermostats appear to work, but are cheap so were replaced anyway.
Shiny grouphead after cleaning Looking good!
If we follow the waters path from the pump, it enters the bottom of the boiler via a rubber tube. This then fills the boiler until the water reaches the top of standing copper pipe that’s purpose is to stop the boiler running dry.
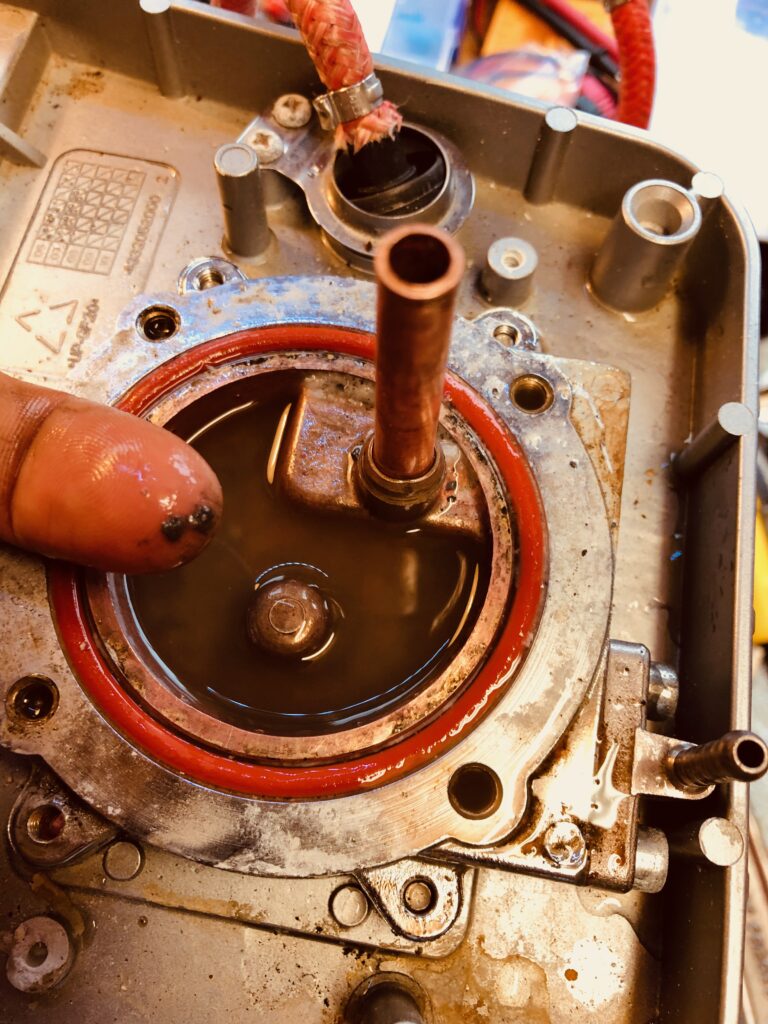
Once the water runs down this pipe it exits the boiler via a small tube and usually immediately reenters the grouphead directly below. This function is permitted via the use of a solenoid. The solenoid is a small diverting device controlled by a coil which is powered by the control board. Without power to the coil the path of the water is permanently blocked to the grouphead.
What is the purpose of the solenoid? Well at the end of your coffee shot the solenoid opens to create a third path for the water to exit up through the top of the solenoid tube via a tube back to the drip tray. This function allows the ‘puck’ of coffee to be dry after you have pulled a shot. This convenience stops the puck being soaked in water, but is largely a nicety we can do without. Many machines, including the later famous Gaggia Classic removed this feature entirely, and for the sake of convenience we too are going to remove it.
So we move on to the long and arduous process of removing the coil from the circuit entirely. This proved to be quite a lot more work than I anticipated.
Removing the solenoid we see its in a pretty bad way:
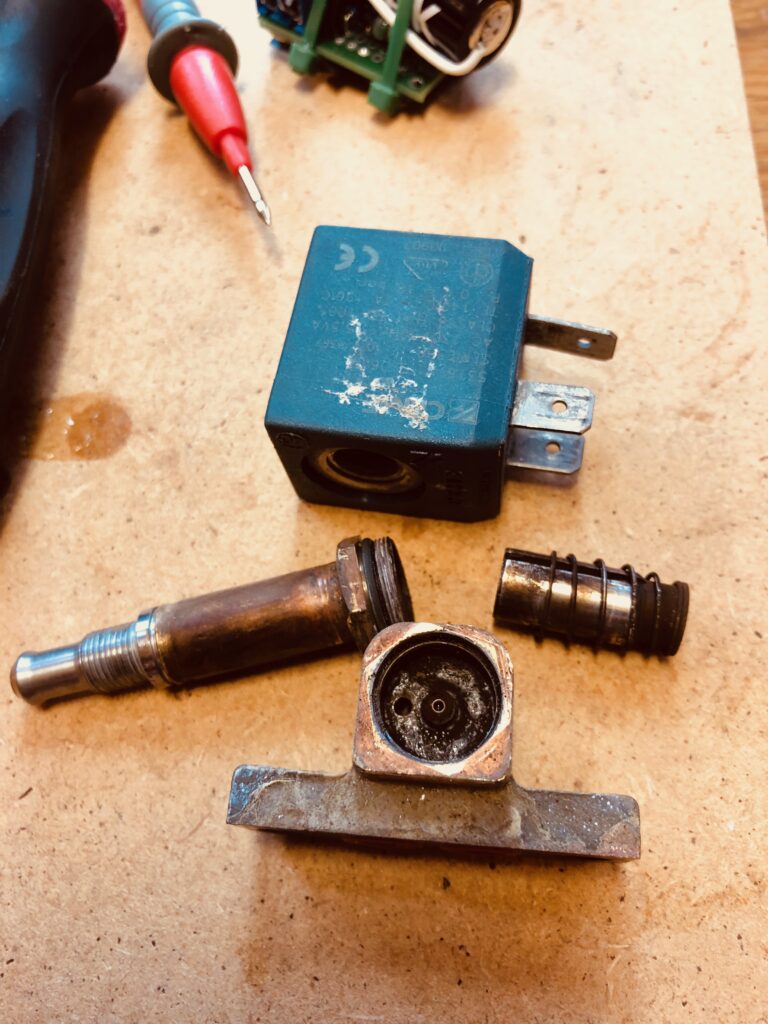
Testing the coil itself shows open circuit. I suspect what ever blew the circuit board also caused the coil to see a large current and act as a fuse. Replacing the coil is a substantial cost even for a used part, and on closer inspection the coil cylinder tube it encapsulates was also cracked. Bad news all round, but none the less we cleaned it all up.
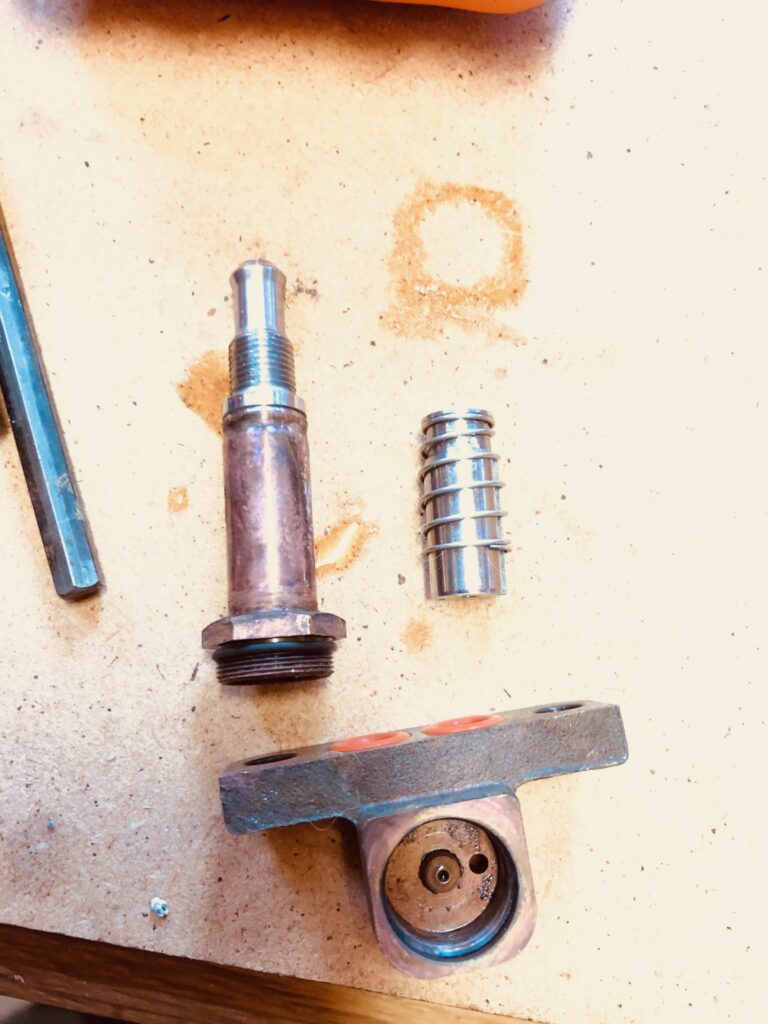
The bottom component above that attaches to the boiler has two holes. The hole on the right side and the centre hole. The water would come up one hole and ideally go back down the the adjacent hole. However this depends on us blocking off the solenoid tube above that allows water to flow back to the drip tray through the now cracked tube.
The problem is this water is pressured at 15 BAR and is not going to be stopped easily. Particularly with a crack in the tube. So what do we do ? It turns out we needed 3 attempts.
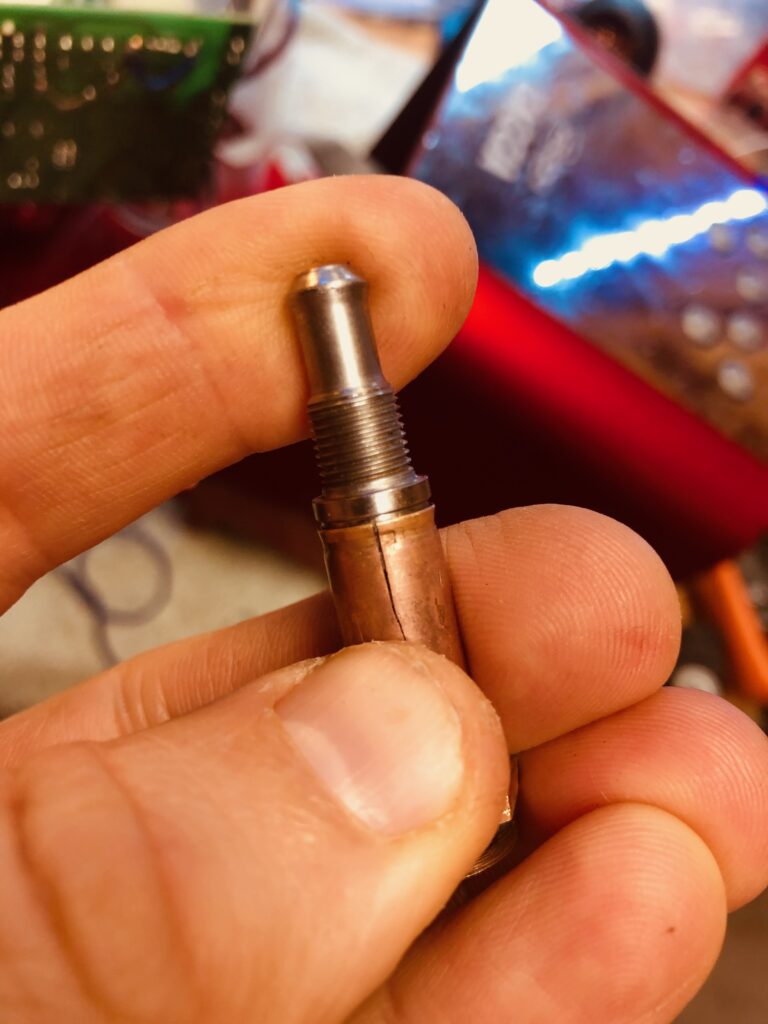
Firstly we tried filling the tube with sealant. This was optimistic and as suspected the sheer pressure of the water forced the sealant both up the tube to the drip tray and through the grouphead. Knife through butter.
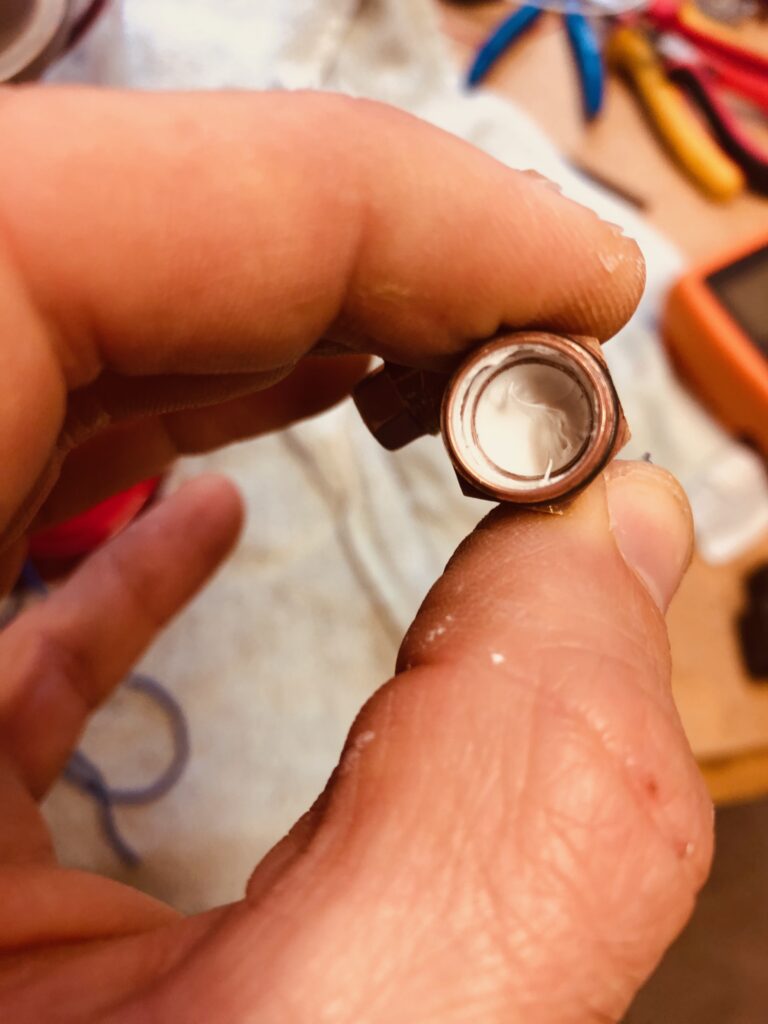
We needed something stronger: Much stronger.
Next was synthetic rubber cork. This was shaped to fit the solenoid tube and forced down the tube entirely blocking the exit. I was confident this would work, and indeed it did. For about 15 minutes. The force of the water stripped the cork into pieces and forced small fragments of it through the grouphead, blocking the internal small pipes in the grouphead itself. This was a major problem and I feared may spell an end to any further attempt at fixing the unit. Even if the water was flowing correctly through the modified solenoid valve, it was now restricted in the grouphead itself which has no easy access.
However, using small pins, and a lot of patience, I was able to extract the small pieces of cork, and there was much relief to see a high force jet of water being emitted from the grouphead, along with several lumps of cork. Even if it was also accompanied by water shooting from the top of the solenoid valve!
With a cracked tube and no easy way of blocking off the tube, I was losing hope we could repair the solenoid valve without replacing the entire part for around £55. However one final attempt involved using Poundland 2 part epoxy. I filled the tube carefully and allowed it to set for 24 hours. Then drilled the top of the epoxy smooth allowing just enough space for the water to move freely from one port to the next without entering the solenoid tube. Success !
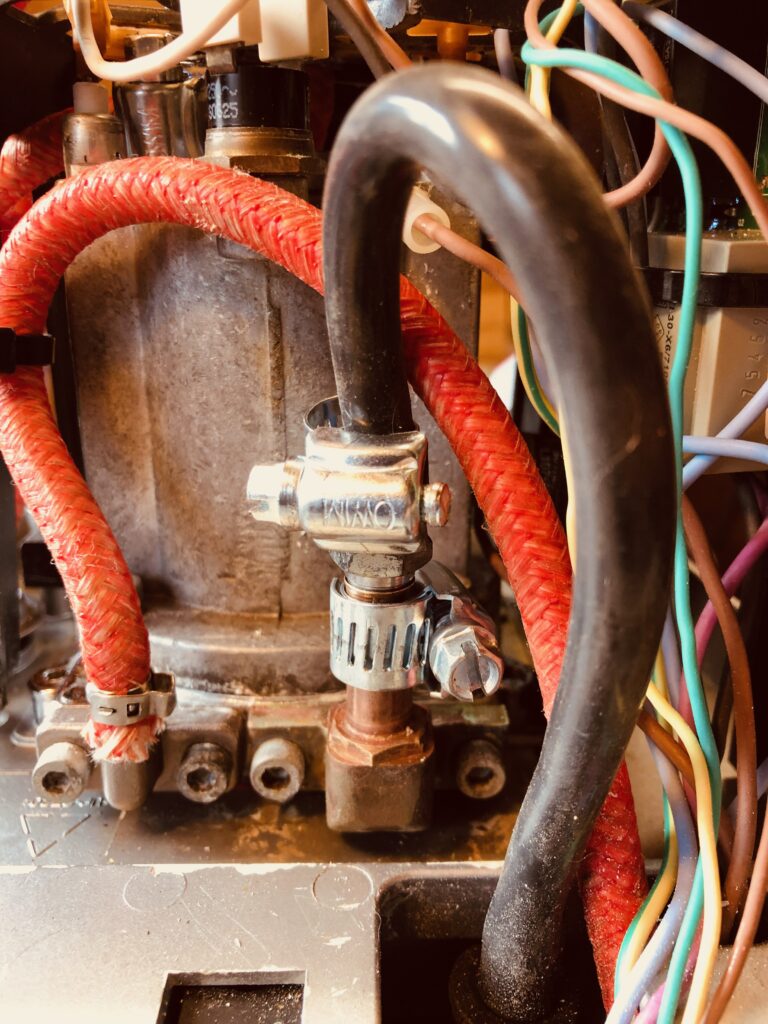
We now had water from the grouphead, but sadly a LOT of leaks. Most of the pipe connections were worn out or were not adequately sealed using jubilee clips when subjected to enormous pressure. Jubilee clips tend to seal with a slight oval shape when tightened, and under pressure this allowed an escape of fluid. We replaced all of the connections with side screw Fuel Hose clips and reinforced the tube seatings with rubber and sealed the joints with PTFE tape. Did it still leak after all this? Yes it did. But only a very small dribble. We can live with it, and the tiny few drops will find their way to the drain holes fine.
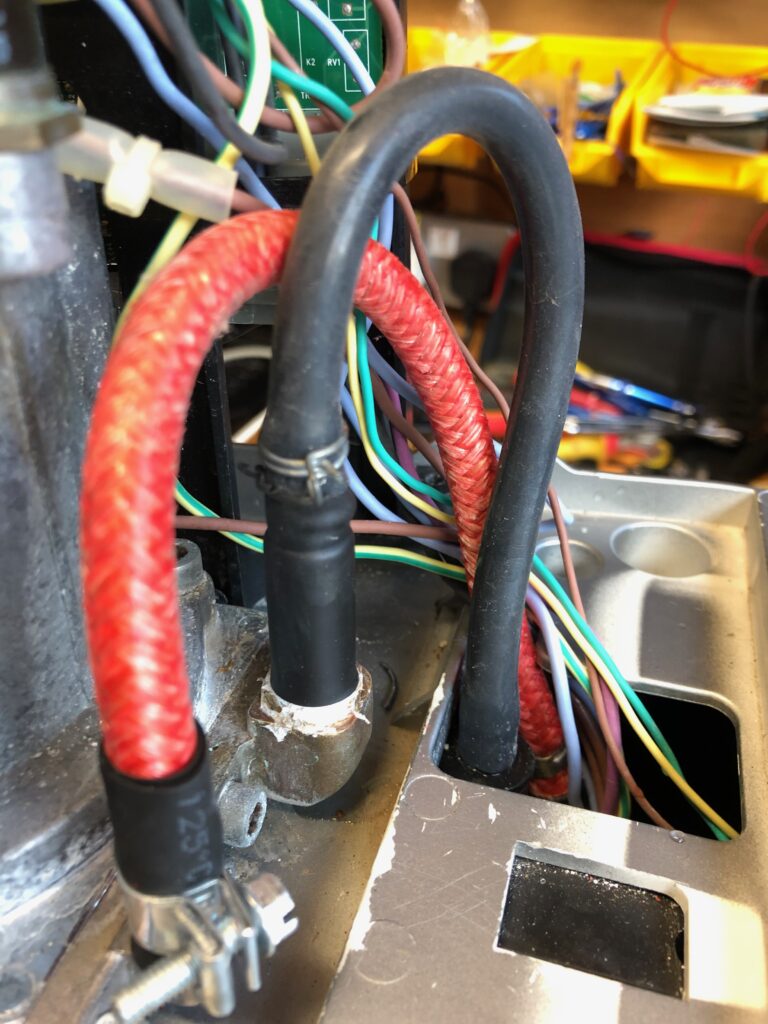
Video: Testing the seals.
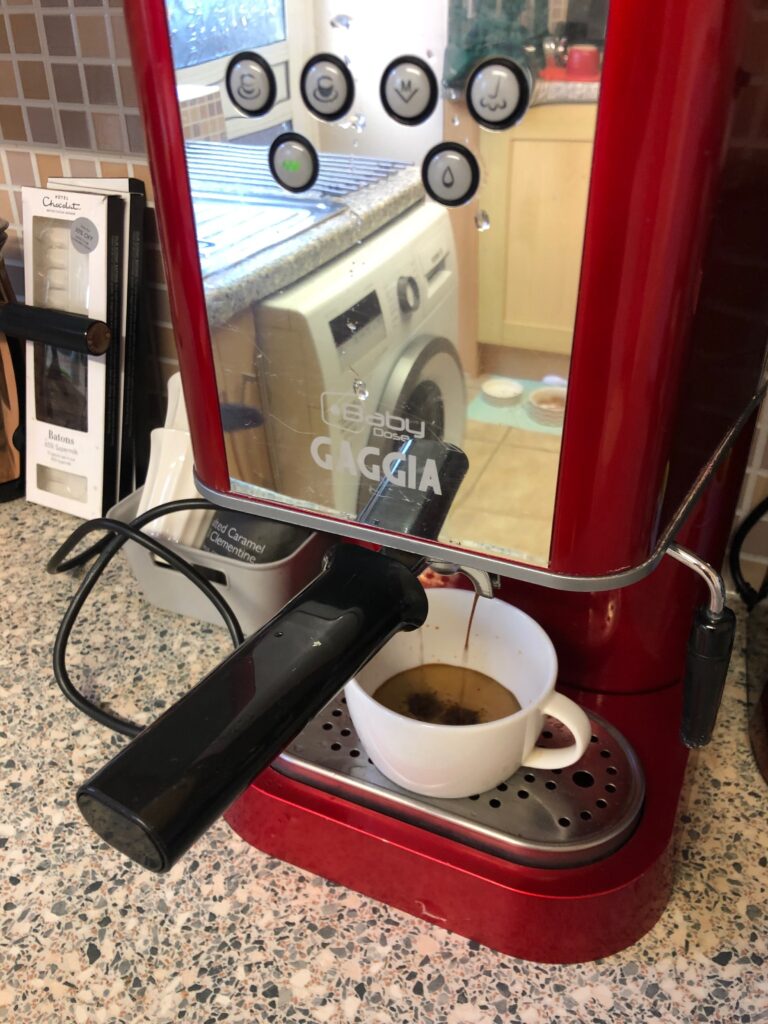
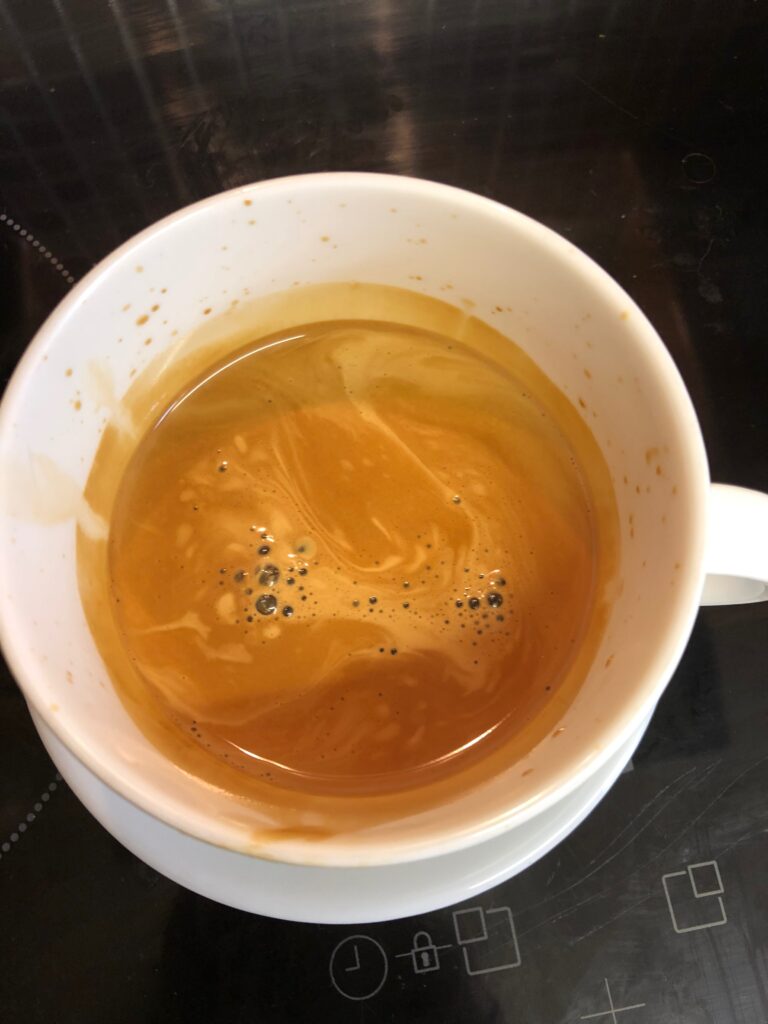
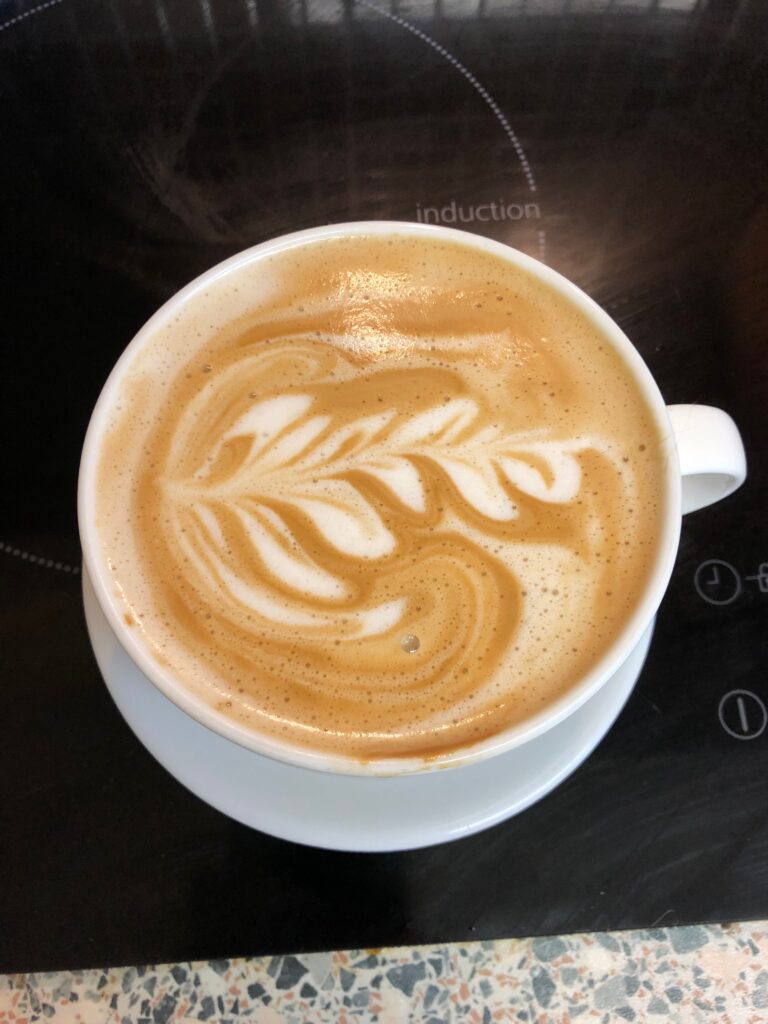
Its been an adventure, but we finally fixed it. It’s fair to say this machine has its share of quirks and will never run like new, but it creates very good coffee and for just £35, its a bargain. 🙂 Thanks for reading. x
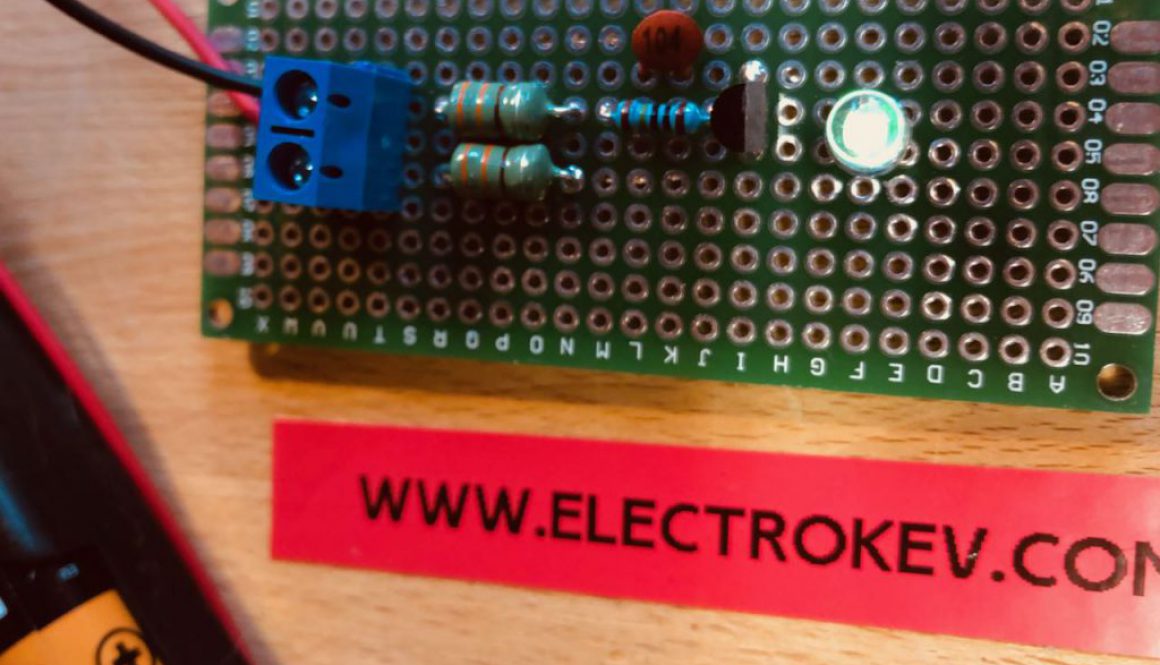
Everlasting ‘Flashing!’ Light
A light that will shine from the moment you are born until you are 18? One single AA battery? Not possible?
The Everlasting light is powerered using the circuit commonly known as the JouleThief. The Joule Thief came to fruition in 1999 when an article by Z. Kapernik was published in the November edition of ‘Everyday Practical Electronics’. Written for the ‘Ingenuity Unlimited’ section of the magazine, the circuit describes a clever little design that utilises almost all of a battery cell. The term ‘Joule Thief’ was coined by Clive Mitchell or BigClive as he is known on his very popular YouTube channel. This is a great channel and I highly recommend it if you enjoy electronics.
Whereas a 1.5 volt battery might be considered ‘Used’ when the voltage drops from 1.5v to maybe 0.9v at best, the Joule Thief carries on functioning right down to around 0.3v. Some advanced versions of the circuit can even drive the cell down to 0.1v.
The following circuit is a modified but simple build of the Joule Thief using Axial coils rather than a traditional wound coil. This makes it very simple for those new to electronics. One of the few difficulties building a Joule Thief is ensuring the coils are wound the correct way. With Axial coils this is not an issue; and so long as the coils are placed side by side, the circuit will work.
There is a wealth of information online regarding the Joule Thief and how it works, but in essence this device is a ‘Blocking Oscillator’ that switches the transistor on and off many thousands of times per second. The coils work together to create a voltage booster, which when paired with an LED appear to show a solidly lit light.
Ordinarily the value of the resistor feeding the base of the transistor would dictate how ‘hard’ the transistor was driven. Often a 1K resistor is used and this will provide a very bright light. In this example, a 10 MegaOhm resistor is used alongside a capacitor to extend the battery life exponentially at the expense of brightness. It’s fair to say the light produced will not light the room, but this project is not about brightness; its about endurance!
The circuit draws just under 13 microamps of power. Considering an AA battery may typically store 2 Million microamp hours of power, this would theoretically drive the LED for 153,846 hours, or 17.56 years. Of course this is very misleading. The battery data sheets that provide this information assume certain power draw characteristics that are more typical than such a low current. It is also quite possible that after 18 years the natural degradation of the battery would see more power loss than the LED load itself. Furthermore, unless extremely high quality batteries were used, its quite possibly the battery would simply leak in that timespan.
But theoretical numbers are what Joule Thieves are all about, and so with that in mind, the project creates a light that will light for almost 18 years. We hope!
This circuit uses simple parts. A single AA battery, and a common NPN transistor. The BC337. LED colours have diferent current draw characteristics, and a green colour has been chosen in this project for its immense efficiency at a low current. The circuit is highly modifiable. Adjustments to the resistor, the inductors, or the capacitor will see different output voltages, light level and longevity.
Keeping the inductors pressed close together will result in a fast flashing light. Creating a tiny gap will speed the flash rate up so fast it will appear as though the light is constantly on.
This project is now available to buy in the Shop as a Kit.
All components supplied, including solder and instructions. All you need is a cheap soldering iron, some time and a small space to build. Have fun 🙂
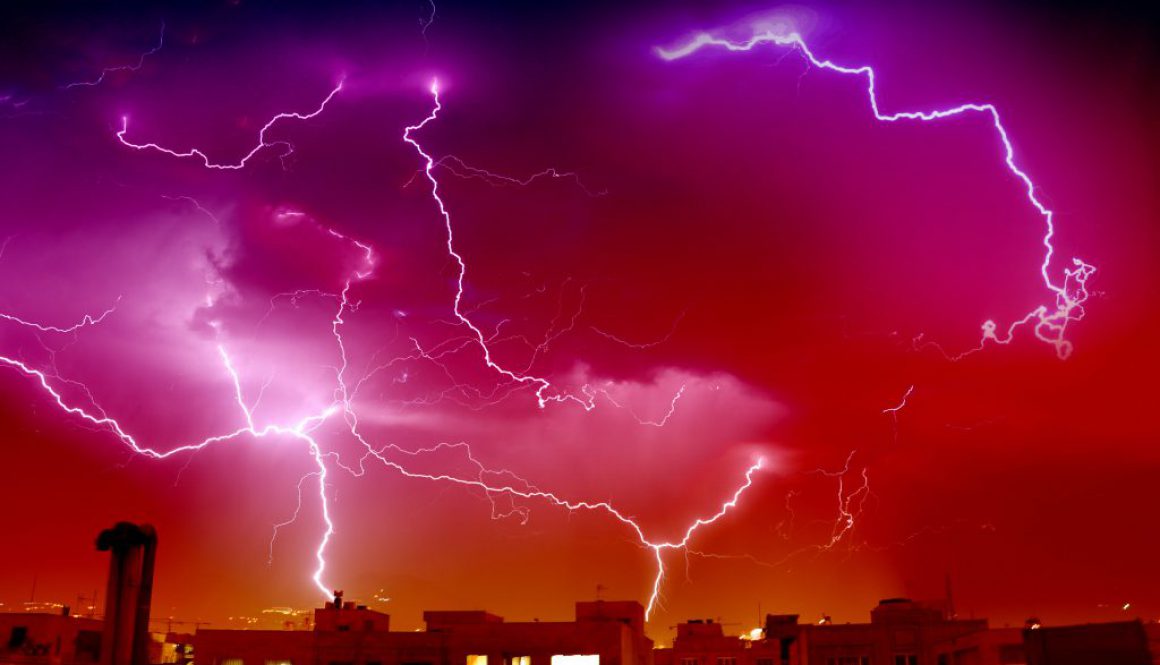
Jacobs Ladder
DO NOT ATTEMPT TO REPRODUCE ANYTHING IN THIS ARTICLE. DANGER OF DEATH. HIGHLY DANGEROUS PROJECT.
Project of the month: Build a high voltage device that will arc bolts of electrical discharge from one electrode to another. This arc should rise up to the top of the device and dissipate before another generates itself at the bottom!
How will it work:
Something like this: a large heavy duty transformer will create 29 volts of direct current at a high ampage.
This relatively low voltage will be fed to a ZVS switch. A Zero Voltage Switch. A ZVS switch will convert the direct current into a high frequency switching DC voltage more suitable for the next stage. The Flyback Coil.
For the coil we are using a FlyBack transformer; the type found in old CRT television sets. This will take the input voltage and scale it up around 1000 times producing a staggeringly high voltage. Many thousands of volts.
This voltage is fed by cable to two large vertical electrodes. The energy potential between them is sufficiently high that a spark will arc from one electrode to the other.
This will occur at the base of the unit as this is where the electrodes are closest together.
As the spark generates enormous heat the spark will start to rise. As it gets hotter and hotter it will rise and rise pulling the gap necessary to leap larger and larger. As the spark reaches the top of the electrode it disappears off the top. Then the process starts all over again.
My brother and I started by creating the projects base. The main electrodes used were braising rods, which we would later find out were not the best idea. These rods are soft metal, with a relatively low melting point. As it turns out the Jacobs ladder makes everything it touches extremely hot and consequently the rods did some melting when the arc didn’t rise as expected.
The rods were easily bent round in a U shape and bolted to the wooden platform with screws and washers. The wires from the Flyback were terminated with crimped on adaptors and screwed down between the washer and the screw.
Unsure what gap to begin testing with, we left around 3/4 inch as this seemed like a good starting point.
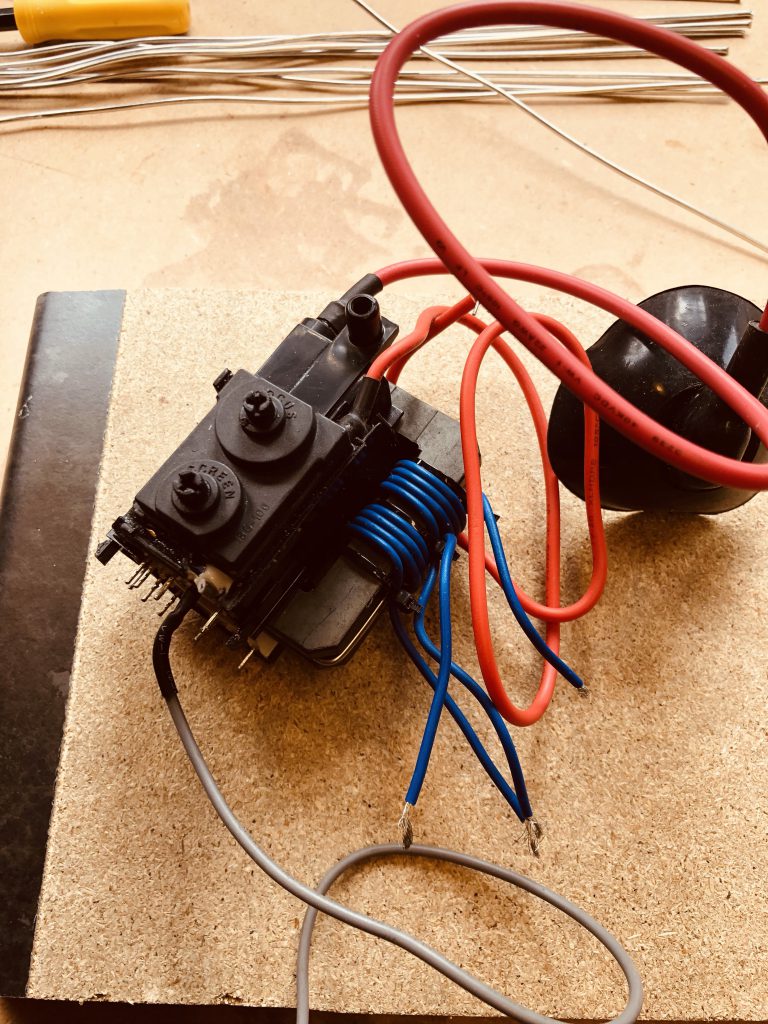
The supplied Flyback transformer had several connectors. A little googling revealed which was the ground and which of the two thick red wires provided the strongest output. Of the two wires, the thicker of the two had a small rubber cup attached to one end. This supposedly connects the Flyback to the CRT tube it was originally designed for. We snipped this off and terminated it with a crimped on spade. The other output was coiled up and the end insulated with heat shrink.
Of the many terminals on the bottom of the Flyback, one had been pre-wired with a grey wire which is the ground cable. This would be attached to one of the electrodes.
All the components were screwed to the wooden base neatly and the wires kept out of each other’s way as best as possible. The electrodes were brought up straight as possible with curved ends to ‘encourage’ the spark to dissipate as it flew off the top.
The power supply was a very old Farnell 24 volt unregulated supply that provides 10amps. The last safety test notice stated 1991, but the old PSU was still working beautifully. The supply actually output 28.8volts unloaded, and as our ZVS demands 12-36 this seemed perfect.
First turning the device on resulted in a arc being generated at the base of the electrodes. The arc did not rise, but a small adjustment to the electrodes gave a great improvement, seeing the arc rise dramatically up the full length of the electrodes.
The Jacobs Ladder ran well for about 3 minutes. There was a sudden cessation with no obvious cause. Adjustments to the primary coil of the Flyback resurrected the device temporarily but I suspect the secondary potted coil of the Flyback has been damaged. Testing the ZVS reveals normal working conditions, so the next step will be to replace the fly back and try and get the JL working again.
Finally, above is a short video of the Flyback rewound with thinner wire, creating a 1 inch arc between two nails.
And below: The moment it died! 🙁
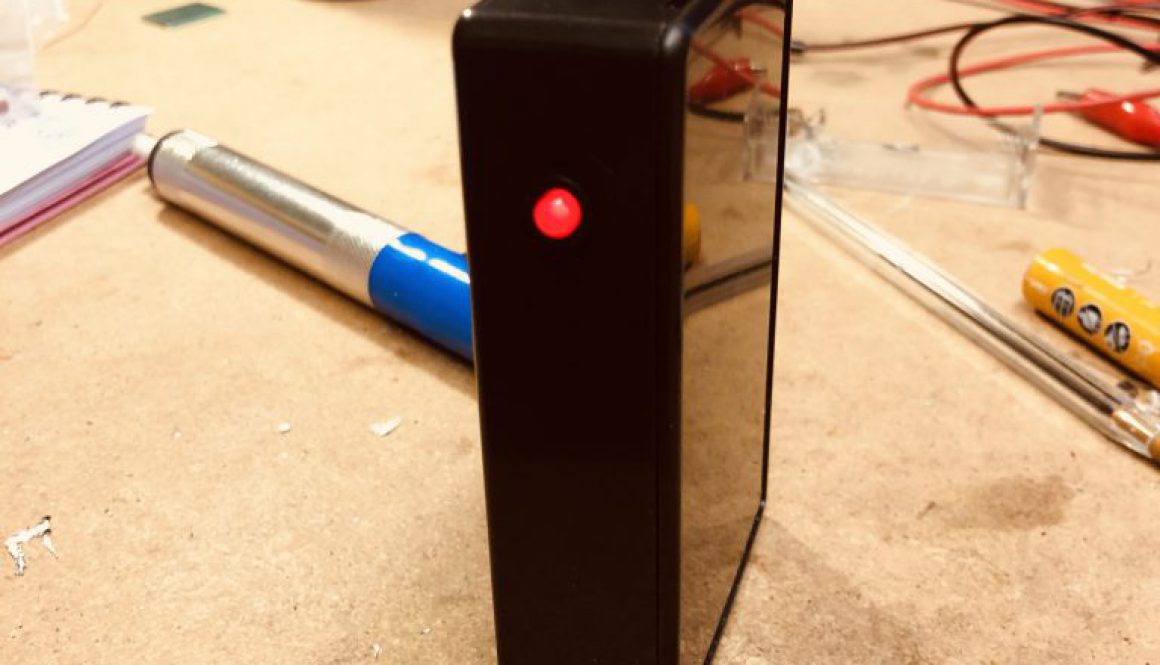
Microwave Body Sensor
The microwave body sensor has been well documented on the internet and tested multiple times. How it works remains a mystery to many, but the set up of this device is very simple. the tiny circuit board has a regulated output, a ground, and a switched live.
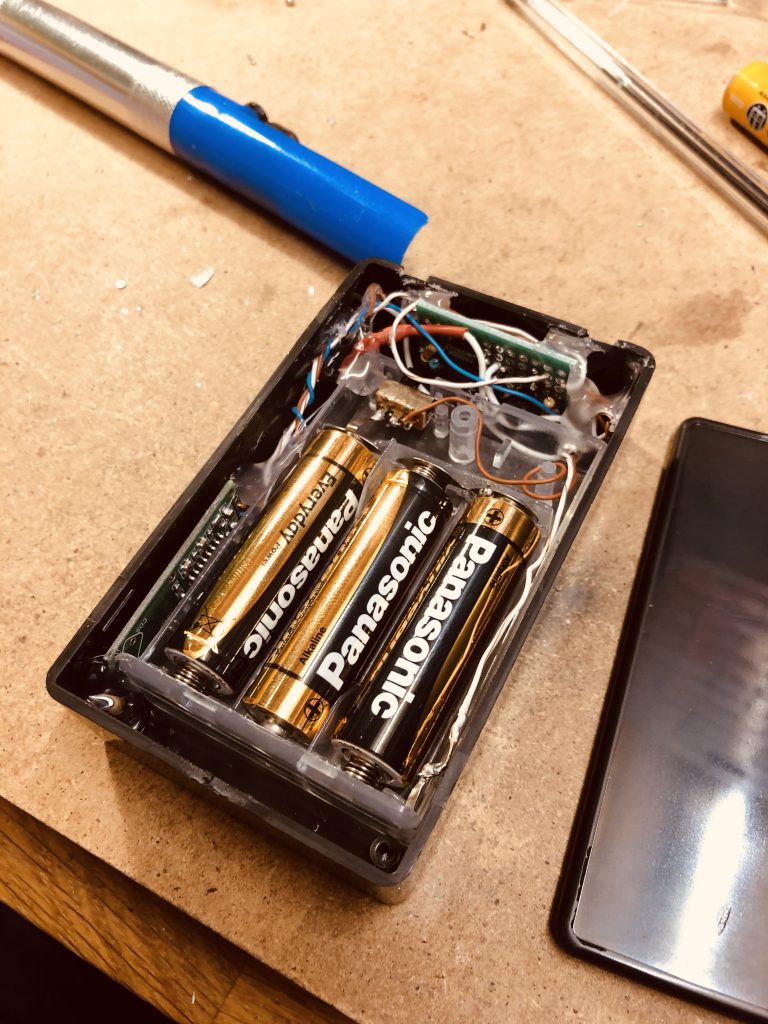
When the microwave sensor detects a body within range it will power the switched live with a low current.
The unit will work approximately 20 feet away, and due to the nature of microwaves will work through walls.
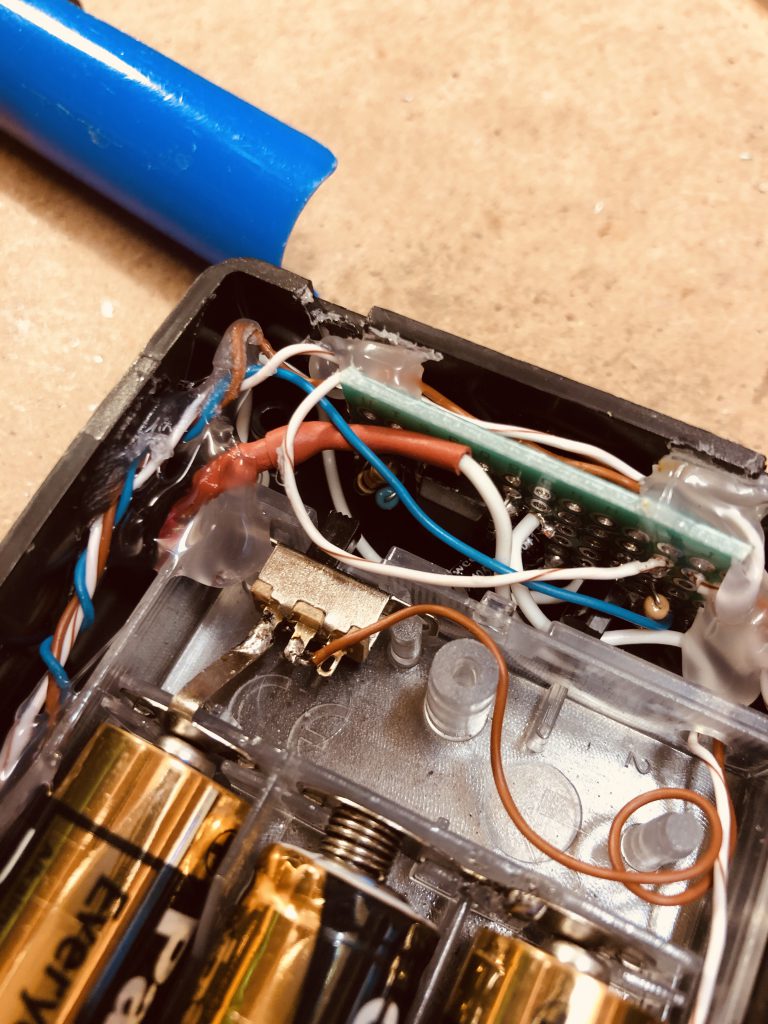
In this project the switched live powers a transistor which in turn switches on a standard 555 set up flashing a red LED.
The entire project is mounted tightly into a small project box with almost the entire space occupied by 3 x AA 1.5v batteries. The microwave circuit is shoehorned down the side of the battery compartment.
In tests the microwave circuit can just about power a 555 circuit directly, but the output is brighter and sharper with a switched transistor.
This unit placed on a shelf will detect movement anywhere in the room, or the room above it.
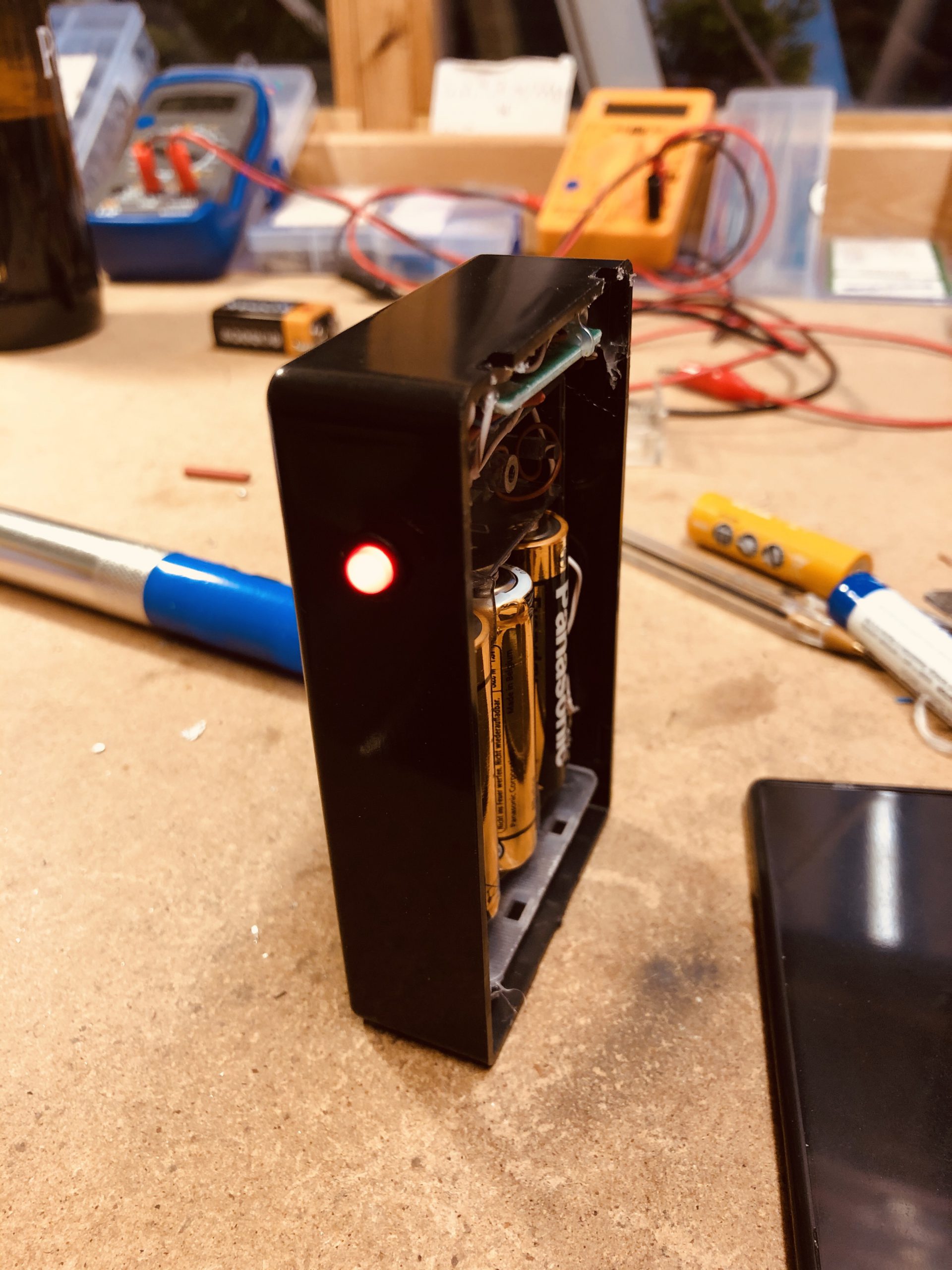
When powered up the unit takes around 5 seconds to stabilise itself during which time the output is switched on.
The Microwave sensor itself draws very little current, with the majority of the current in this circuit being drawn by the 555.